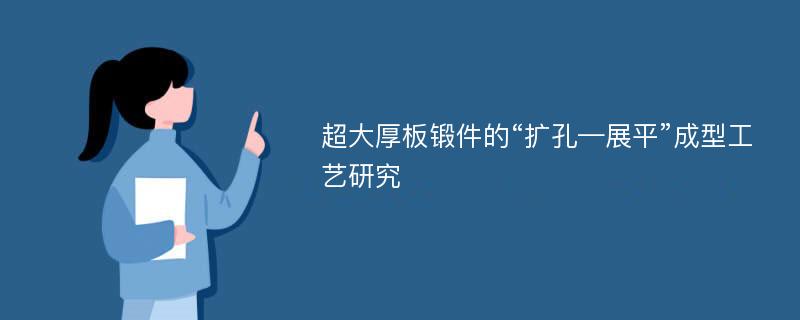
论文摘要
随着大型核电、石化等工业的发展,一些大型、超大型厚板类锻件的需求量越来越大、性能要求越来越高。这些锻件在使用过程中常处于高应力状态,不仅制造精度要求高,还需要有很高的机械性能。目前大型锻件一般采用铸锭自由锻成型,成型过程中需要有足够的塑性变形量使铸态组织转化为致密的锻态组织,并使金属流线合理分布。但对于超大型锻件的成型,由于尺寸及重量等方面的原因,传统锻造加工工艺与设备很难达到预期的效果,须采取特殊的生产、加工工艺措施。例如,中国二重公司开发的800MN压力机的关键结构部件——“C”型板,就属于超大且形状较复杂的厚板类锻件,常规方法几乎无法成型。“扩孔-展平”工艺是一种在现有设备条件下生产超大厚板的独特工艺方法。该方法首先将空心铸坯芯轴扩孔至具有一定厚度的圆筒锻件,然后对其进行纵向剖切,再经过展平等工序得到所需尺寸的成品件。本文对超大厚板的“扩孔-展平”工艺过程进行了研究,主要工作包括:①根据现有生产条件,综合分析了“C”型板的成型方案;②大型圆筒锻件芯轴扩孔成形的理论分析常常采用平面应变的假设,本文采用物理模拟及数值模拟方法,研究了该假设的适应性;③制定了生产“C”型板所需的圆筒件扩孔加工方案,分析了影响变形的各种因素;④应用数值模拟方法分析了大型筒形锻件的芯轴扩孔工艺,从而确定合理的工艺参数;⑤分析了圆筒锻件的纵向剖切以及剖切后弧形锻件的“展平”工艺。通过上述研究,对超大厚板类锻件的“扩孔-展平”加工方法有了深入的认识,相关结论可用于指导实际生产。
论文目录
中文摘要英文摘要1 绪论1.1 引言1.2 超大厚板类锻件的加工工艺概述1.3 国内外研究与发展现状1.4 论文选题的目的及意义1.5 主要研究内容1.6 研究的可行性2 800MN 液压机“C”型板及其锻造成型方案2.1 800MN 液压机“C”型板2.2 “C”型板几何形状参数分析2.3 本章小结3 平面应变假设的适用条件3.1 芯轴扩孔变形的特点3.2 坯料计算3.3 长轴类筒形锻件变形的平面应变变形模式3.3.1 平面应变压缩的理论分析3.3.2 平面应变的塑性变形实验3.3.3 实验过程及结果3.3.4 实验数据处理3.3.5 不同的下压量对圆形截面坯料变形的影响3.3.6 塑性平面应变变形的数值分析3.4 本章小结4 芯轴扩孔热锻参数的确定及模拟分析4.1 DEFORM 概述4.2 模拟参数4.2.1 材料成分及性能4.2.2 扩孔芯轴的选取4.2.3 上砧压下量的确定4.2.4 芯轴转动角度的确定4.2.5 热传导边界条件的设定4.2.6 坯料与芯轴相对运动的设定4.2.7 坯料与芯轴及上砧间接触条件的设定4.2.8 液压机上砧运行速度的设定4.2.9 液压机上砧行程4.2.10 始锻和终锻温度4.2.11 流动应力模型及屈服准则4.3 芯轴扩孔热锻模拟分析4.3.1 有限元模型的建立4.3.2 上砧压下量对圆筒坯料变形区的影响4.3.3 坯料的轴向变形4.3.4 上砧第二次下压后的坯料翻转角度4.3.5 上砧第二次下压后的应变分布4.4 各个锻造周期完成后的应变分布4.4.1 第一锻造周期4.4.2 第二锻造周期4.4.3 第三锻造周期4.5 本章小结5 超大非对称厚板的展平工艺分析5.1 展平原理5.2 圆柱滚压展平数值模拟分析5.2.1 有限元模型的建立5.2.2 模拟结果分析5.3 本章小结6 结论致谢参考文献附录A. 作者在攻读硕士学位期间发表的论文目录
相关论文文献
标签:成型论文; 大型厚板锻件论文; 扩孔论文; 展平论文; 数值模拟论文;