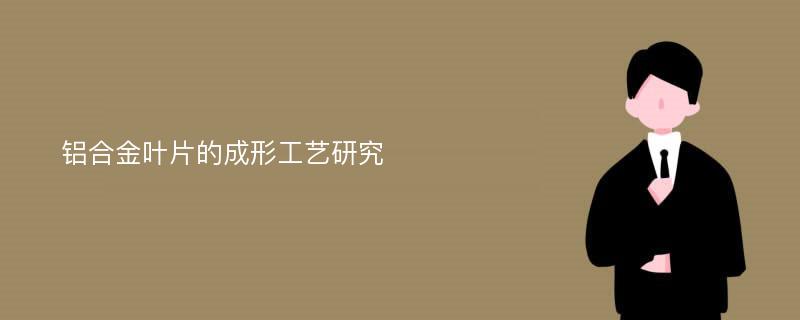
论文摘要
本文所研究的铝合金叶片是某产品上的重要零件,外形形状比较简单,尺寸精度要求高,性能有一定要求。对于此类零件,目前国内一直用一定厚度的铝合金板材直接进行机械加工的方式制造。另外,也常用铝合金型材挤压的方式制造,即将铝合金板材直接热挤压后,切割出零件上的两个凸台。这两种制造方法材料、能源消耗大,生产成本高,不仅不符合节能降耗的发展要求,同时难以满足产品性能方面的要求。针对这些问题,本文对铝合金叶片进行了用“等温挤压”方法的研究。根据零件的结构特征,对成形工艺进行分析。应用三维有限元数值模拟软件DEFORM,在建立简化模型基础上,分析了等温挤压成形过程中金属流动规律。首先讨论了凹模有无飞边槽对零件成形的影响,同时模拟了不同坯料形状以及坯料在凹模中放置于不同位置时的挤压情况。在此基础上分析了挤压过程中的金属流动、等效应力和载荷-行程曲线的变化。在上述研究的基础上,设计了挤压模具,并进行了实验研究。结果表明:制定的工艺方案可行性好,设计的模具使用合理,金属流动均匀,零件充填效果较好,产品精度和性能均达到技术要求,抗拉强度可以达到480Mpa,为该类零件的工程化应用奠定了基础。
论文目录
摘要ABSTRACT第1章 绪论1.1 课题研究背景及意义1.2 铝合金的相关研究概况1.2.1 铝合金的国外研究现状1.2.2 铝合金的国内研究现状1.3 温挤压技术的概况及特点1.3.1 温挤压技术概况1.3.2 等温挤压技术的特点1.4 铝合金挤压技术概况及发展现状1.4.1 铝合金挤压技术概况1.4.2 铝合金挤压技术的发展1.5 限元法的发展和研究现状1.5.1 发展概况1.5.2 有限元法在塑性加工领域的应用1.6 本课题主要研究内容第2章 成形工艺分析2.1 引言2.2 所选材料的分析2.3 挤压件图的制定2.4 工艺方案的制定2.4.1 制定工艺方案的原则2.4.2 制定工艺方案2.5 小结第3章 等温挤压的数值模拟3.1 有限元法简介3.1.1 刚塑性材料的基本假设3.1.2 刚塑性材料的基本方程3.2 模拟软件DEFORM 简介3.2.1 软件概述3.2.2 软件的模块结构3.3 模拟方案的提出3.3.1 模拟条件和模拟模型的建立3.3.2 模拟结果及分析3.4 等温挤压的模拟和结果分析3.4.1 坯料模型的建立和模拟条件3.4.2 模拟结果和结果分析3.5 小结第4章 工艺制定和模具设计4.1 铝合金叶片的温挤压工艺制定4.2 挤压工艺参数选择4.2.1 挤压温度4.2.2 挤压速度4.2.3 挤压过程中的润滑4.3 工艺参数的确定4.3.1 下料尺寸的计算4.3.2 挤压力的确定4.4 模具材料的选择4.5 模具设计4.5.1 凸模结构设计4.5.2 凹模结构设计4.5.3 顶出装置的设计4.6 小结第5章 实验研究5.1 引言5.2 实验条件5.2.1 实验设备5.2.2 材料5.2.3 实验模具5.2.4 润滑5.3 实验过程5.3.1 下料5.3.2 模具组装5.3.3 预热5.3.4 挤压成形5.3.5 热处理和后续加工5.4 零件成形的关键问题5.5 成形后零件性能分析5.6 小结结论参考文献攻读硕士学位期间发表的论文致谢
相关论文文献
标签:铝合金论文; 叶片论文; 等温挤压论文; 三维有限元模拟论文; 飞边槽论文; 抗拉强度论文;