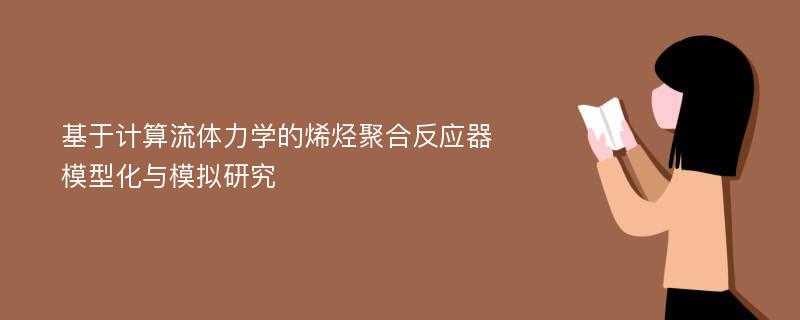
论文摘要
聚合反应器技术的创新是基于对反应器中的物理传递过程(动量、热量和质量传递)和聚合反应过程的深入理解。通过实验手段解析聚合反应器中的传递和化学反应过程时,装置的建立需要耗费大量精力,实验工作量大,并且因为测量手段的限制,很难对温度分布和产品空间分布等物理量进行测量。通过计算流体力学(CFD)方法可获得非理想反应器中的浓度、速度、温度分布与化学反应过程规律,节省大量的人力物力。然而在烯烃聚合反应器中,体系的复杂性(多相流操作、介质粘度高)、传递与化学反应过程的耦合、聚合反应动力学的复杂性都使CFD模型的建立成为难题。因此对聚合反应器内的传递和化学反应过程进行模型化,促进研究方法论的进步,富有挑战性的同时又具有工业应用前景和十分重要的学术价值。论文针对烯烃聚合反应器,采用CFD方法建立耦合混合流动过程、热量传递过程和化学反应过程的CFD模型,并通过模拟研究取得了以下创新性结果:(1)针对气相搅拌流化床反应器,建立了基于颗粒动力学理论的双流体模型,并与多重参考坐标系的方法相结合,通过CFD模拟与实验相结合的方法揭示了搅拌桨转动对流态化的影响规律。径向流桨对流化床的床层压降影响不大,但足够大的搅拌速度可以显著减小压力脉动的幅值与气泡尺寸,提高流化质量。按照搅拌对流态化的影响程度不同,可将流化床由下至上分为三个区域:入口区,搅拌流态化区和自由流态化区。气体分布器的作用在入口区占优势,搅拌桨的转动可使搅拌流态化区的流态化质量得到明显改善。对自由流态化区而言,搅拌桨的作用不明显。(2)通过CFD模拟及对压力脉动的实验研究,揭示了Geldart D类颗粒在搅拌流化床中的流型转变规律。大粒径的Geldart D类颗粒出现了只有Geldart A类颗粒才具有的散式流态化现象。在搅拌桨的作用下,颗粒的最小流化速度基本不变,而最小鼓泡速度随搅拌桨转动而增加,散式流态化的气速操作范围随搅拌桨转速的增加而变大。由聚式流态化向散式流态化转变的过程是将“搅拌减小气泡尺寸”的量变转化为“无气泡化”的质变的过程。(3)通过考察工业尺度乙烯气相聚合流化床反应器内的温度分布与流态化和传热过程的相互关系,揭示反应器内温度分布不均匀性产生的根本原因。基于双流体模型与颗粒动力学理论,通过用户自定义编程(UDF)描述热量传递方程,对流动和传热规律进行考察,发现在流化床底部形成一对颗粒循环流,使气体分布器上方的颗粒主要沿径向运动,轴向方向上的混合质量较差,床层出现了较大的温度梯度。循环流使温度较低的颗粒沿循环流的交汇处上升,形成低温区。(4)在以中高粘度流体为介质的搅拌釜式反应器中,通过UDF建立有限速率/涡耗散-卷吸(FR/ED-E)微观混合模型,通过预测平行竞争反应的选择性考察微观混合情况。模拟结果表明,当搅拌槽中流体粘度较低、搅拌桨旋转速度较大以及进料位置处于搅拌桨的排出区时,微观混合质量好,副产物的选择性小。反应区域由于对流、卷吸、变形和扩散等过程而体积膨胀,同时由于化学反应的消耗而体积缩小,两因素共同作用,使反应区域的体积达到最大值后减小。模型参数通过实验值的回归得到,受流体粘度影响较大,而对于同一种非牛顿流体,在不同搅拌桨转速下,模型参数取相同的值即可得到与实验工作相符性较好的反应选择性。可利用此特性进行反应器的设计、放大和优化,从实验室中取得参数值,将其用于预测工业反应器中的传递与化学反应过程。
论文目录
致谢摘要Abstract目录插图清单插表清单1 绪论2 文献综述2.1 典型烯烃聚合反应装置分析2.1.1 Unipol乙烯聚合工艺的气相流化床2.1.2 Hypol丙烯聚合工艺的气相流化床2.1.3 烯烃溶液聚合的搅拌釜式反应器2.2 气固流态化研究2.2.1 聚式流态化2.2.2 散式流态化2.2.3 最小鼓泡速度测量2.2.4 压力脉动2.2.5 计算流体力学研究进展2.3 流态化过程强化2.3.1 静止内构件2.3.2 振动流态化2.3.3 磁场流态化2.3.4 声场流态化2.3.5 搅拌流态化2.3.5.1 搅拌流化床的流态化规律2.3.5.2 搅拌流化床的应用2.4 流化床中的热量传递过程2.4.1 气固两相的温度分布2.4.2 热量传递过程的影响因素2.5 传递与化学反应过程的CFD模型2.5.1 均相反应体系2.5.1.1 微观混合2.5.1.2 反应流模型2.5.2 气固两相反应体系2.5.2.1 臭氧分解反应2.5.2.2 复杂化学反应体系2.6 课题提出与研究目标3 基于CFD方法的气固两相流模型化3.1 双流体模型3.2 颗粒动力学理论3.3 气固曳力模型3.4 气固两相流的模拟方法3.4.1 几何模型的建立3.4.2 计算区域的划分3.4.3 控制方程的离散化3.4.4 计算模型的选择3.4.5 边界条件的设定3.5 搅拌流态化建模3.5.1 多重参考坐标系方法3.5.2 模拟方法3.5.3 模型验证3.6 热量传递过程建模3.6.1 能量守恒方程3.6.2 聚合反应释放的热量3.6.3 求解方法3.6.4 模型验证3.7 聚合反应过程建模3.8 小结符号说明4 搅拌流化床的实验与CFD模拟研究4.1 实验部分4.2 搅拌对流态化的影响规律4.2.1 床层压降与最小流化速度4.2.2 压力脉动4.2.2.1 搅拌桨转速4.2.2.2 床层高度4.2.2.3 径向位置4.2.3 颗粒速度4.2.4 固含率4.2.4.1 固含率脉动4.2.4.2 固含率分布4.3 搅拌流化床中的散式流态化现象4.3.1 最小鼓泡速度4.3.2 颗粒速度分布4.3.3 固含率分析4.4 小结符号说明5 工业尺度流化床的热量传递过程5.1 工业流化床反应器5.2 聚乙烯粉末冷模试验5.2.1 床层压降5.2.2 床层膨胀高度5.2.3 压力脉动5.3 CFD结果与讨论5.3.1 流态化过程5.3.2 2D/3D模拟结果对比5.3.3 颗粒速度分布5.3.4 温度分布5.3.5 传热过程分析5.4 小结符号说明6 气相流化床中耦合聚合反应动力学的CFD模拟方法探索6.1 乙烯聚合动力学机理模型和矩方法6.2 CFD数学模型6.3 模拟方法6.4 结果与讨论6.4.1 小尺度等温流化床6.4.1.1 流化过程6.4.1.2 颗粒速度分布6.4.1.3 分子量空间分布与多分散指数6.4.1.4 动力学常数的影响6.4.1.5 氢气浓度的影响6.4.1.6 反应器温度的影响6.4.2 大尺度非等温流化床6.5 小结符号说明7 搅拌釜式反应器中的微观混合与化学反应过程7.1 化学反应体系的选择7.2 模拟条件7.3 CFD数学模型建立及求解策略7.3.1 湍流模型7.3.2 有限速率/涡耗散-卷吸模型的建立7.3.3 参数确定7.3.4 求解策略7.4 结果与讨论7.4.1 液滴离散数7.4.2 不同操作条件下微观混合情况与反应选择性7.4.3 反应区域演化7.4.4 反应-混合过程7.5 小结符号说明8 结论和展望8.1 结论8.2 研究展望8.3 论文的主要创新点参考文献作者简介及攻读博士学位期间主要研究成果
相关论文文献
标签:烯烃聚合反应器论文; 多相流论文; 搅拌流化床论文; 计算流体力学论文; 热量传递论文; 流态化论文; 矩方法论文;