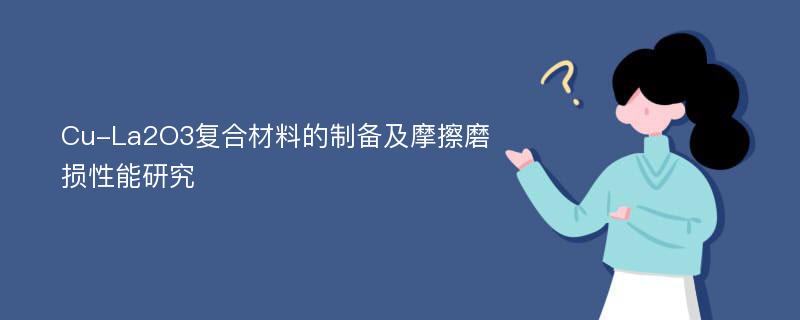
论文摘要
高强高导材料在机械、航空航天等行业有着极为广泛的用途,如电力机车受电弓、电磁发射装置轨道材料、电刷等,它们要求材料不仅具有高导电性,而且要具有较高的耐磨性。由于纯铜是传统的高导电材料,但其强度低耐热性差,大大限制了其应用范围。本文采用内氧化结合热挤压的方法制备出了高导电高耐磨性的Cu-La2O3复合材料,采用扫描电子显微镜(SEM)、透射电子显微镜(TEM)和X射线衍射分析仪(XRD)等微观手段,系统研究了载荷、滑动速度和电流等对Cu-La2O3复合材料摩擦磨损行为的影响,揭示了摩擦副的磨损机制,为高性能耐磨铜基复合材料的应用提供理论与实验依据。通过对不同La2O3含量的复合材料性能测试,系统研究了压制压力、烧结温度和增强体含量对材料物理性能和力学性能的影响。研究结果表明Cu-1.3wt%La2O3复合材料的硬度和导电率在900℃时达到峰值;当温度进一步升高时,由于烧结体内颗粒长大,使材料性能下降。随La2O3含量的增加,复合材料的硬度和拉伸强度升高,而导电率降低,当La2O3质量含量超过1%时,导电率低于80%IACS。对不同电流、载荷和速度条件下复合材料的摩擦磨损行为进行了研究。载流条件下,磨损率均随载荷的增加出现先降低而后增加的“U”型变化趋势。随着滑动速度的增加,最佳载荷相应的降低,此现象未见文献报道。电流、速度、载荷和距离等的综合作用使基体材料软化,磨损损失增大。Cu-La2O3复合材料在低载荷,高滑动速度和电流条件下的磨损形貌以电弧烧蚀、液滴飞溅和塑性变形为主要特征。在摩擦热、焦耳热及电弧热的共同作用下接触区内的接触点熔融甚至蒸发,并在摩擦副之间发生材料转移。磨损过程为氧化磨损、磨粒磨损、粘着磨损、疲劳磨损和电弧烧蚀等多种磨损机制共同作用的结果。研究了Cu-La2O3复合材料的高速摩擦磨损行为。结果表明:随着La2O3含量的增加,复合材料的磨损率降低。La2O3的加入不仅提高了复合材料的耐磨性,而且延缓了严重磨损的发生。在复合材料的轻微磨损阶段,机械混合层的形成与部分破裂导致的氧化磨损和磨粒磨损为主要的磨损机制;在严重磨损阶段,剥层磨损和粘着磨损成为主要的磨损机制,复合材料磨损表面具有划痕、塑性变形、粘着等主要特征。磨损过程包括材料转移、亚表层塑性变形及磨屑与磨损表面的机械混合等。研究了机械混合层对复合材料摩擦磨损行为的影响。结果发现:机械混合层的形成率和断裂率决定了复合材料的磨损行为,它存在于整个的轻微磨损阶段。随着载荷的增加,机械混合层的硬度和厚度均增大。不同La2O3含量的复合材料其磨损率发生突变的临界载荷随着机械混合层厚度的增加而增大,但随机械混合层硬度增大而减小,硬度大而薄的机械混合层具有大的转变载荷。研究了真空及低温条件下Cu-La2O3复合材料的摩擦磨损行为。随着滑动距离的增加,首先摩擦系数急剧升高出现摩擦系数的最高值,而后降低并在一定的范围内波动。随着载荷的增加,不同滑动速度下的磨损率均呈现出增加的趋势。当超过一定的滑动速度时,磨损率将发生突变,且随载荷的增加,发生突变所对应的速度减小。Cu-La2O3复合材料在真空中的磨损机制主要为粘着磨损。复合材料磨损表面具有犁沟、塑性变形和粘着等特征。轴承钢上存在大量的粘着转移物,形成明显的材料转移层,在真空磨损过程中,复合材料与转移层之间存在材料间的相互转移。
论文目录
摘要Abstract第1章 绪论1.1 铜基复合材料概述1.2 颗粒增强铜基复合材料的制备工艺及性能1.2.1 颗粒增强铜基复合材料的制备工艺1.2.2 颗粒增强铜基复合材料的性能1.3 颗粒增强金属基复合材料的摩擦磨损行为的研究进展1.3.1 基体种类1.3.2 增强物种类1.3.3 增强物尺寸1.3.4 增强物含量1.3.5 载荷1.3.6 滑动速度1.3.7 载流磨损1.3.8 环境条件1.3.9 磨损机制1.4 本研究工作内容及意义第2章 材料制备及研究方法2.1 材料制备2.2 分析测试方法2.2.1 密度测量2.2.2 X 射线衍射分析2.2.3 扫描电镜分析2.2.4 透射电镜分析2.2.5 硬度测量2.2.6 拉伸性能测试2.2.7 导电性能测量2.2.8 摩擦磨损性能测试2.3 本章小结第3章 铜基复合材料的设计及性能3.1 复合材料的设计203复合材料制备工艺的研究'>3.2 Cu-La203复合材料制备工艺的研究3.2.1 实验原料3.2.2 压制压力的选择3.2.3 复合材料烧结工艺的确定203 复合材料的性能'>3.3 Cu-La203复合材料的性能3.3.1 硬度及相对密度3.3.2 导电性能3.3.3 拉伸性能3.4 本章小结第4章 Cu-La203复合材料干摩擦磨损性能研究4.1 引言4.2 实验材料及方法203 复合材料摩擦磨损实验结果'>4.3 Cu-La203复合材料摩擦磨损实验结果4.3.1 载荷对复合材料摩擦磨损行为的影响4.3.2 滑动速度及距离对复合材料摩擦磨损行为的影响4.4 分析与讨论4.5 机械混合层的形成与断裂4.6 磨损亚表面及磨屑分析4.6.1 磨损亚表面观察4.6.2 磨屑观察与分析4.7 机械混合层的厚度及硬度分析4.7.1 机械混合层的厚度与载荷的关系4.7.2 机械混合层的硬度与载荷的关系4.7.3 临界载荷对材料机械混合层临界厚度及硬度的影响203 复合材料的磨损机理'>4.8 Cu-La203复合材料的磨损机理4.8.1 轻微磨损阶段4.8.2 严重磨损阶段4.9 本章小结第5章 载流条件下Cu-La203复合材料摩擦磨损性能研究5.1 引言5.2 实验参数5.3 载荷对复合材料摩擦磨损性能的影响203 复合材料摩擦系数的影响'>5.3.1 载荷对Cu-La203复合材料摩擦系数的影响203 复合材料磨损率的影响'>5.3.2 载荷对Cu-La203复合材料磨损率的影响5.3.3 不同载荷下的磨损表面形貌观察5.3.4 载荷对摩擦磨损性能影响的分析与讨论5.4 滑动速度对复合材料摩擦磨损性能的影响203复合材料摩擦系数的影响'>5.4.1 滑动速度对Cu-La203复合材料摩擦系数的影响203复合材料磨损率的影响'>5.4.2 滑动速度对Cu-La203复合材料磨损率的影响5.4.3 不同滑动速度下的磨损表面形貌5.4.4 速度对摩擦磨损性能影响的分析与讨论5.5 电流对复合材料摩擦磨损性能的影响203复合材料摩擦系数的影响'>5.5.1 电流对Cu-La203复合材料摩擦系数的影响203复合材料磨损率的影响'>5.5.2 电流对Cu-La203复合材料磨损率的影响5.5.3 不同电流下的磨损表面形貌观察5.5.4 电流对摩擦磨损性能影响的分析与讨论5.6 载流摩擦磨损分析5.7 载流摩擦磨损机理5.8 本章小结第6章 Cu-La203复合材料真空中的摩擦磨损性能研究6.1 引言6.2 实验材料及参数203复合材料在真空中的摩擦系数'>6.3 Cu-La203复合材料在真空中的摩擦系数6.3.1 真空中摩擦系数随滑动距离的变化6.3.2 载荷和滑动速度对真空摩擦系数的影响6.3.3 真空和大气中的摩擦系数对比203复合材料在真空中的磨损率'>6.4 Cu-La203复合材料在真空中的磨损率6.4.1 真空和大气中磨损质量随滑动距离的变化6.4.2 载荷和滑动速度对真空磨损率的影响6.5 真空条件下的磨损表面6.6 真空条件下的磨屑分析6.7 分析与讨论6.8 本章小结结论参考文献攻读学位期间承担的科研任务与主要成果致谢作者简介
相关论文文献
标签:铜基复合材料论文; 摩擦磨损论文; 载流论文; 电弧论文; 真空环境论文; 低温论文;