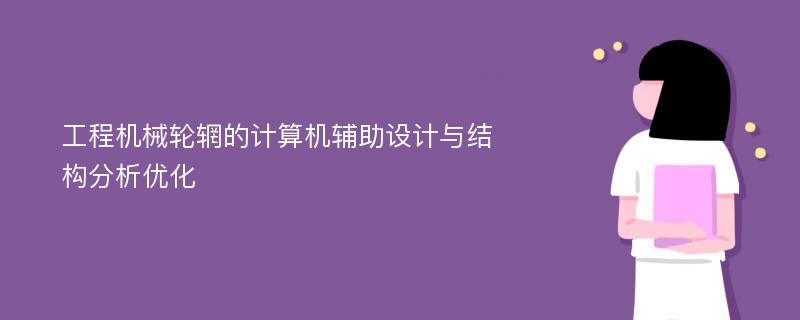
论文摘要
目前产品可靠性、安全性、市场反映敏捷性、资源能源指标、环境指标等成为企业重要的竞争指标,而我国工程机械轮辋与国外同类产品甚至国内其他行业产品都有很大差距。针对国内工程机械轮辋产品安全性、可靠性、市场反映敏捷性和系统理论支持少的现状,本文主要针对轮辋体受载情况及强度情况进行了分析研究,对轮辋体设计的CAD系统进行了研究,并在此基础上对轮辋进行了结构优化,对轮辋体的疲劳分析和寿命预估进行了分析研究,并在合作单位山东工程机械钢圈厂进行了推广应用。首先对装载机的不同工况进行分析,建立了不同工况下的轮辋受载力学模型,研究了轮辋体受载的具体理论依据;并对不同工况下轮辋体的载荷分布情况进行了计算分析,确定了不同工况下的负荷情况及重点校核对象。在此基础上分析了轮辋体受载情况和边界条件,计算轮辋体的具体载荷并确定了轮辋体的边界条件;通过ABAQUS对轮辋体的工作情况进行分析,得出了各种工况下的应力和位移云图,找出了轮辋体结构的薄弱点和强度储备过强的部分,并通过实验对仿真结果进行了验证。建立了轮辋的三维模型,并通过分析轮辋各部分的具体尺寸关系,开发出轮辋设计的计算机辅助系统。基于Solid Edge平台利用VB开发的轮辋设计的计算机辅助系统依据厂方要求开发,具有很强实用性,此系统可以对已有类型零件进行三维参数化设计,并且具有很强的扩展性,能添加新的其它类型零件的设计系统。此系统经厂家使用反馈,可以大大减轻设计人员的负担,缩短新产品开发时间,提高生产效率,效果良好。在前面研究基础上,利用建模准确性、轮辋计算机辅助系统建模的快捷性和有限元仿真有效性,对轮辋体进行了结构优化,并对厂家的产品进行了仿真分析。对轮辋体在轮辋厚度和轮辐的位置两方面进行了不同尺寸规格的有限元仿真,并通过分析找出了尺寸的最合理位置,对轮辋体结构进行了优化,使轮辋体的材料储备强度得到了有效利用;对山东省工程机械轮辋厂的许多产品进行了应力应变及位移的分析,成功计算出轮辋在工作过程的安全系数,为轮辋的强度计算提供了理论依据。结合传统疲劳失效分析方法和Miner疲劳损伤线性积累理论,提出了一种分析轮辋体疲劳强度和寿命预估的新方法。并利用此方法计算出轮辋体的条件疲劳极限,并最终基于Miner疲劳损伤线性积累理论对轮辋体在不同工况下进行了疲劳强度的检验和寿命预估。本课题为山东大学可持续制造中心与山东工程机械钢圈厂合作的校企合作项目。
论文目录
CONTENT摘要ABSTRACT第1章 绪论1.1 课题研究背景1.1.1 工程机械在国民中的地位1.1.2 轮式装载机发展现状1.1.3 工程机械面临的机遇和挑战1.1.4 轮辋优化的重要性1.2 课题研究目的及意义1.2.1 课题的提出1.2.2 课题研究的目的和意义1.3 课题的主要研究内容及结构体系1.3.1 研究内容1.3.2 论文组织结构第2章 装载机轮辋力学模型的建立及求解2.1 LG950-1装载机简介2.1.1 装载机LG950-1的主要性能2.1.2 装载机LG950-1的标准配置2.2 装载机轮辋力学模型的建立及求解2.2.1 空载工况下装载机轮辋的力学模型2.2.2 负载行走工况下装载机轮辋的力学模型2.2.3 极限正载工况下装载机轮辋的力学模型2.2.4 极限偏载载荷下装载机的力学模型2.2.5 工作地面倾斜时装载机轮辋的力学模型2.3 各工况下装载机轮辋的受力比较与分析2.4 本章小结第3章 装载机轮辋的静态分析3.1 有限元分析方法概述3.1.1 有限元分析实施步骤3.1.2 有限元分析特点3.1.3 ABAQUS简介3.2 轮辋实体建模3.2.1 装载机轮辋简介3.2.2 轮辋的三维模型建立3.3 轮辋体载荷分布及边界条件分析3.3.1 轮辋体的边界情况3.3.2 轮辋体载荷分布情况3.3.3 轮辋载荷的具体计算3.4 轮辋体在ABAQUS中的有限元仿真3.4.1 有限元仿真过程3.4.2 各工况下轮辋体的位移、应力云图3.4.3 结果分析3.5 轮辋应力应变实验3.5.1 试验目的3.5.2 试验器具3.5.3 试验内容3.5.4 试验方法3.5.5 实验步骤3.5.6 有限元结果对比3.6 本章小结第4章 轮辋设计的计算机辅助系统开发4.1 系统总体介绍4.1.1 系统的内涵及特点4.1.2 系统的结构体系4.1.3 系统开发基础4.2 系统开发流程4.2.1 轮辋三维模型建立4.2.2 轮辋尺寸关系及主要参数确定4.2.3 主要尺寸与其它尺寸的约束关系确定4.2.4 软件功能的实现4.3 轮辋体设计系统应用实例4.3.1 系统用户群和环境要求4.3.2 轮辋设计实例4.3.3 软件测试4.4 本章小结第5章 轮辋的结构优化及应用5.1 优化方案的确定5.2 轮辋轮辐位置的分析优化5.2.1 分析优化方案确定5.2.2 分析优化过程5.3 轮辋厚度的分析优化5.3.1 分析优化方案确定5.3.2 分析优化过程5.4 分析仿真的实施应用情况5.5 本章小结第6章 轮辋的疲劳强度分析与寿命预估6.1 疲劳强度设计方法概述6.1.1 疲劳定义6.1.2 国内外研究现状6.2 抗疲劳设计方法分析6.2.1 传统抗疲劳设计方法6.2.2 Miner疲劳损伤线性积累理论6.2.3 本文采用的轮辋疲劳分析方法6.3 轮辋的疲劳强度分析及寿命预估6.3.1 影响机械零件疲劳强度的因素6.3.2 轮辋体的条件疲劳极限计算6.3.3 基于Miner疲劳理论的轮辋体使用寿命预估6.4 本章小结第7章 结论与展望参考文献致谢攻读学位期间发表的学术论文及参加的科研项目学位论文评阅及答辩情况表
相关论文文献
标签:工程机械论文; 轮辋论文; 参数化设计论文; 结构分析优化论文; 疲劳论文;