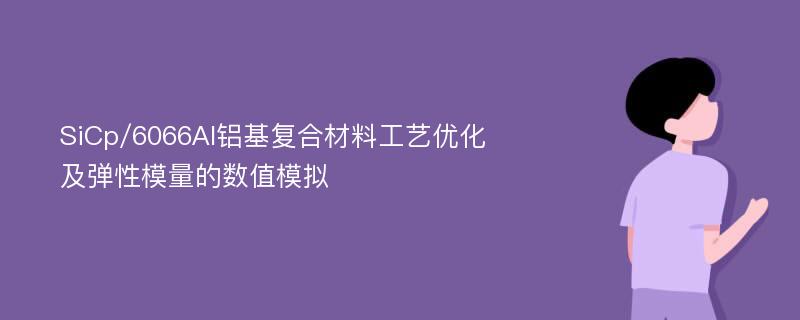
论文摘要
碳化硅颗粒增强铝基复合材料具有高比强度和比刚度、耐磨、耐疲劳、低热膨胀系数、低密度、高微屈服强度、良好的尺寸稳定性和导热性等优异的力学性能和物理性能,可广泛应用于航空航天、军事、汽车、电子、体育运动等领域。目前,各国相继进入了碳化硅增强铝基复合材料的应用开发阶段,在美国和欧洲发达国家,该类复合材料的工业应用也已开始,并且被列为21世纪新材料应用开发的重要方向。国内有多家单位正在研究碳化硅颗粒增强铝基复合材料,并取得一定的进展。制约该种复合材料广泛应用的重要原因之一在于其弹性模量不能符合应用的要求。因此开发高弹性模量的碳化硅颗粒增强铝基复合材料,有重要的应用价值。本文以保证拉伸性能尤其是延伸率的前提下提高SiCp/6066Al复合材料弹性模量为主要研究对象,以复合材料微观力学为理论工具,通过复合材料制备、拉伸性能和弹性模量测试,金相组织、拉伸断口、界面形貌等组织观察,利用宏-微观统一本构模型对复合材料弹性模量进行数值模拟,揭示影响复合材料弹性模量的决定性因素。本文采取包套热挤压粉末冶金工艺成功制备了高弹性模量的SiCp/6066Al复合材料。研究中发现:为了制得达到预期性能的SiCp/6066Al复合材料,适宜的SiC颗粒体积分数为12%,而520℃/20min+水淬+170℃/5h的热处理制度为较优越的热处理制度,对复合材料的抗拉强度、屈服强度以及相对延伸率的提高都为有利。文中分析了不同SiCp/6066Al复合材料金相显微组织中颗粒分布的均匀性,结果表明:颗粒分布越均匀,越有利于复合材料拉伸性能的提高。另外,从纵向金相显微组织中观察到SiC颗粒具有沿挤压方向流动特征。本文确定了10vol.%SiCp/6066Al复合材料的断裂模式为延性断裂,而15vol.%SiCp/6066Al复合材料的拉伸断口则表现为脆性和延性混合断裂模式。文中将复合材料的断裂机制划分为基体的韧性断裂、颗粒与基体间的界面脱粘、颗粒与基体间的界面开裂、SiC颗粒团聚体的脆性开裂以及单个SiC颗粒的脆断。不同界面结合情况下,起主要作用的机制不同。通过TEM观察发现,铝基复合材料弹性模量的差异是由基体和增强体之间的界面结合力不同导致的。界面上一定厚度的反应层、离散分布其上的沉淀相增强了界面结合力。SiC颗粒与基体间的反应层不是Al4C3层。界面结合机制不是扩散结合,而是化学反应结合。为了确定众多参数影响复合材料弹性模量的规律,本文建立了适用于颗粒增强金属基复合材料的宏-微观统一本构模型及宏-微观一体化分析方法。该模型能够
论文目录
中文摘要英文摘要1 绪论1.1 引言p/Al 合金复合材料的优异性能及其应用'>1.2 SiCp/Al 合金复合材料的优异性能及其应用p/Al 合金复合材料的性能'>1.2.1 SiCp/Al 合金复合材料的性能p/Al 合金复合材料的应用'>1.2.2 SiCp/Al 合金复合材料的应用p/Al 合金复合材料的制备工艺'>1.3 SiCp/Al 合金复合材料的制备工艺1.3.1 搅拌铸造法1.3.2 粉末冶金法1.3.3 浸渗铸造法1.3.4 喷射成形法p/Al 合金复合材料的微观结构'>1.4 SiCp/Al 合金复合材料的微观结构1.4.1 增强相1.4.2 位错1.4.3 晶粒结构1.4.4 时效析出相p/Al 合金复合材料的显微损伤'>1.5 SiCp/Al 合金复合材料的显微损伤1.5.1 基体破坏1.5.2 增强相断裂1.5.3 界面破坏p/Al 合金复合材料的界面'>1.6 SiCp/Al 合金复合材料的界面1.6.1 界面定义1.6.2 复合材料中颗粒与基体的界面1.6.3 复合材料中颗粒与基体的界面相容性1.6.4 界面结合类型和特点1.6.5 对界面的要求p/Al 合金复合材料的时效热处理'>1.7 SiCp/Al 合金复合材料的时效热处理1.7.1 研究复合材料及其基体合金的时效动力学曲线1.7.2 研究复合材料及其基体合金的时效析出序列1.7.3 界面反应对时效析出(硬化)行为的影响p/Al 合金复合材料的强化机制'>1.8 SiCp/Al 合金复合材料的强化机制1.8.1 微观力学强化机制1.8.2 微观结构强化机制1.9 本文研究目的、主要研究内容和技术路线1.9.1 研究目的1.9.2 主要研究内容1.9.3 技术路线p/6066Al 复合材料的工艺优化'>2 SiCp/6066Al 复合材料的工艺优化p/6066Al 复合材料的制备'>2.1 SiCp/6066Al 复合材料的制备2.1.1 实验原材料2.1.2 制备工艺2.2 实验方法2.2.1 拉伸实验2.2.2 弹性模量测量2.2.3 拉伸断口观察2.2.4 组织观察2.3 实验结果和分析2.3.1 拉伸实验2.3.2 拉伸结果讨论2.3.3 弹性模量测量2.4 本章小结p/6066Al 复合材料的组织评价'>3 SiCp/6066Al 复合材料的组织评价p/6066Al 复合材料的金相显微组织'>3.1 SiCp/6066Al 复合材料的金相显微组织p/6066Al 复合材料的拉伸断口形貌'>3.2 SiCp/6066Al 复合材料的拉伸断口形貌p/6066Al 复合材料拉伸断裂行为'>3.2.1 SiCp/6066Al 复合材料拉伸断裂行为3.2.2 基体6066Al 拉伸断口形貌p/6066Al 复合材料拉伸断口形貌'>3.2.3 SiCp/6066Al 复合材料拉伸断口形貌p/6066Al 复合材料的界面'>3.3 SiCp/6066Al 复合材料的界面3.4 本章小结4 颗粒增强金属基复合材料弹性模量预测模型4.1 基本理论4.1.1 代表体积单元4.1.2 有效性能4.1.3 特征应变4.2 复合材料的有效性能预测模型4.2.1 解析模型4.2.2 数值模型4.3 宏-微观统一本构模型4.3.1 引言4.3.2 复合材料宏观量与微观量的联系4.3.3 宏-微观统一本构模型的建立4.3.4 多单元的宏-微观统一本构模型4.4 本章小结p/6066Al 复合材料性能预测系统开发'>5 SiCp/6066Al 复合材料性能预测系统开发5.1 颗粒增强金属基复合材料力学性能预测系统图形用户界面5.1.1 复合材料组分性能输入区5.1.2 复合材料细观结构选择区5.1.3 复合材料细观结构图形示意区5.1.4 多单元宏细观统一本构模型预测结果显示区5.1.5 上下限模型预测结果比较区5.2 颗粒增强金属基复合材料力学性能预测系统计算方法5.2.1 颗粒形状5.2.2 排列方式5.2.3 颗粒尺寸变化方式5.2.4 刚度矩阵、柔度矩阵及其与工程弹性常数间的关系5.3 宏—微观统一本构模型的验证5.4 本章小结p/6066Al 复合材料性能预测结果与分析'>6 SiCp/6066Al 复合材料性能预测结果与分析6.1 影响铝基复合材料弹性模量的因素分析6.2 弹性模量与界面结合的关系p/6066Al 复合材料性能预测结果与分析'>6.3 SiCp/6066Al 复合材料性能预测结果与分析6.3.1 理想界面时影响复合材料弹性模量的因素6.3.2 弱界面时界面性能对复合材料弹性模量的影响分析6.4 颗粒增强金属基复合材料弹性模量预测模型的简化与改进6.5 本章小结7 全文结论致谢参考文献附录 A1 GUIINPUT2 GUISelectShape3 GUISelectArray4 GUISelectDistribution5 GUIShape6 GUIFigureShape7 GUIArray8 GUIMAINPROGRAM9 GUIGMC10 GUIVoigtReuss11 GUIHashinShrikman附录 B
相关论文文献
标签:碳化硅论文; 铝基复合材料论文; 组织论文; 性能论文; 界面论文; 弹性模量论文; 模型论文;
SiCp/6066Al铝基复合材料工艺优化及弹性模量的数值模拟
下载Doc文档