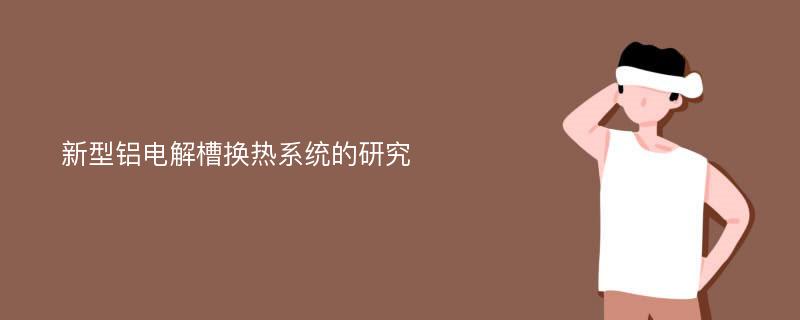
论文摘要
目前,尽管每吨铝的直流电耗已经降低到13000-14000kW·h,但是铝电解的能量利用率却只有40%左右。很多学者从降低平均槽电压和提高电流效率角度对铝电解节能降耗做了深入的研究。但从能量平衡角度分析,在铝电解中有50%左右的电能是以热能的形式散发到环境中的,其中电解槽的顶部散热48%,侧部散热43%,底部散热9%。为实现铝电解过程中的节能降耗的目标,本文对电解槽侧部余热的回收及其影响因素进行了研究。本文首先对铝电解槽的能量平衡、电解槽的散热分布和电解槽的散热方式进行了分析,全面的设计了本实验的新型余热回收式电解槽结构,选择了适合本实验的换热介质。然后在以焦炭为发热体的电解槽中研究了换热熔盐流量和输入功率对回收功率和回收效率的影响。在输入功率不变的条件下,在一定范围内增加或减少换热熔盐流量时,回收功率和回收效率也随着增加或减少。在换热熔盐流量不变的条件下,在一定范围内增加或减少电解槽的输入功率时,回收功率也随着相应的增加或减少,但回收效率确实随着输入功率的增加而减少的,随着输入功率的减少而增加的。最后在铝电解过程中研究了换热熔盐的流量对回收功率和回收效率的影响。电解时,电解温度为900℃,电流效率为90%,电流在1865A-2056A范围内波动,电压在11.53V-12.36V内波动。在维持稳定电解的条件下,当换热熔盐的流量增加时,回收功率和回收效率均增加。当换热熔盐的流量为135.5 cm3/s,回收功率的平均值为9890W,回收效率为41.9%,完全达到了铝电解过程中余热回收的效果。
论文目录
摘要Abstract第一章 绪论1.1 铝电解节能意义1.2 铝电解节能措施1.2.1 大型槽的推广1.2.2 低温铝电解的研究1.2.3 阴极技术的改进1.2.4 阳极技术的的进步1.2.5 新槽型的设计1.2.6 新装置的开发1.2.7 其它节能工艺与措施1.3 铝电解槽散热分布与节能降耗1.3.1 铝电解槽散热分布1.3.2 余热回收研究现状1.4 本课题的主要研究内容第二章 新型余热回收式铝电解槽的设计2.1 电解槽能量平衡2.1.1 电解槽的电压平衡2.1.2 电解槽的能量平衡2.2 电解槽散热2.2.1 电解槽散热计算2.2.2 电解槽散热分布2.2.3 电解槽散热方式2.3 电解槽的设计2.3.1 电流密度2.3.2 槽膛深度2.3.3 阳极到槽帮的距离2.3.4 阴极结构2.3.5 电解质的选择2.3.6 电解槽炉帮厚度计算和碳化硅砖厚度计算2.4 电解槽内换热器的设计计算2.4.1 换热器尺寸的计算2.4.2 换热介质的选择2.4.3 换热熔盐流速的计算2.4 电解槽内侧部保温转厚度的设计计算2.5 电解槽炉底的保温结构设计2.6 铝电解槽和换热器的结构2.6.1 铝电解槽的结构2.6.2 换热器结构2.6.3 换热器上热电偶的分布2.6.4 整个系统的流程2.6.5 辅助设备—熔盐炉选型第三章 电解槽焦粒发热过程余热回收3.1 工业上的焙烧方法3.1.1 炭粒焙烧法3.1.2 铝液焙烧法3.1.3 燃料焙烧法3.1.4 焙烧方法的选择3.2 熔盐流量的变化对温度的影响3.2.1 熔盐流量的变化对电解槽内换热器温度的影响3.2.2 熔盐流量的变化对换热器熔盐进出口温度的影响3.3 回收功率和流量的关系3.3.1 回收功率的计算3.3.2 回收功率与熔盐流量的关系3.4 回收功率与输入功率的关系3.5 本章小结第四章 电解过程电解槽余热的回收4.1 铝电解槽的启动4.1.1 干式启动4.1.2 常规启动4.1.3 本实验铝电解槽启动4.2 电解过程电解槽余热回收4.3 铝电解发热和焦炭焙烧发热过程的余热回收比较4.4 本章小结第五章 结论参考文献致谢
相关论文文献
标签:节能论文; 能量平衡论文; 余热回收论文; 铝电解论文; 熔盐流量论文; 输入功率论文; 回收功率论文; 回收效率论文;