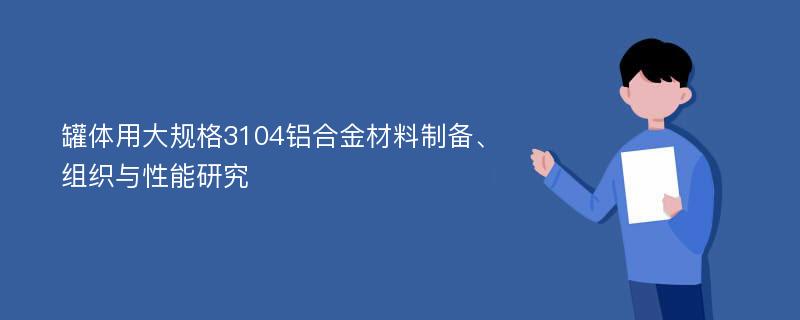
论文摘要
本文结合中国铝业公司科技基金项目,以易拉罐罐体用3104铝合金材料为研究对象,从现场生产线上取样,采用显微硬度、拉伸力学试验、金相、X射线衍射、扫描和透射电子显微分析以及JMatPro软件模拟,对大规格铸锭特性及其均匀化处理、热轧、冷轧等全流程关键工艺控制因素进行研究,在此基础上,深入探讨了3104铝合金薄带成分-组织结构和性能之间的关系。获得了以下创新性成果:(1)3104铝合金大规格铸锭横截面上明显的宏观偏析,从铸锭表面到中心,各元素含量差别很大,Ti含量极差达到0.025%,Mg含量的极差达到0.34%,Ti元素的偏析规律与其他元素相反。从铸锭表层到中心,晶粒和初生化合物尺寸逐渐增大。3104铝合金大规格铸锭横截面上不同部位的微观偏析也是不均匀的,铸锭表层晶内Mg分布较均匀,而铸锭中部存在Mg的晶内偏析。大规格铸锭必须均匀化。(2)随均匀化温度的升高和时间的延长,晶粒内部的偏析逐步减少,显微硬度趋于一致;晶内发生(AlMnSi)和(AlMnFeSi)化合物析出,在590℃以下温度均匀化后析出不均匀,晶界和晶粒中心析出少;600℃以上均匀化后,析出相长大,密度减小,在晶内分布更为均匀。与此同时,晶粒边界区域的铝化物逐步溶解、熔断和球化,部分Al6(FeMn)相转变为α-Al12(MnFe)3Si相;大生产条件下3104合金铸锭最佳均匀化处理工艺为600℃/8-12h。(3)热轧过程过程中化合物的破碎效果非常明显,但热粗轧板坯在厚度和宽度方向上的组织还存在不均匀性,表层为完全再结晶组织,中心部位为热轧变形组织,中间过渡层为部分再结晶组织。经过热精轧后,热轧带材整个断面基本上是完全再结晶组织。(4)热精轧终轧温度和冷却速度对热精轧带材的组织有明显影响,终轧温度愈高、冷却速度愈慢,立方织构含量愈高。终轧温度为340℃和冷却速度为1℃/min时,立方织构含量从热粗轧板坯的30%左右提高到热精轧带材的60%以上。(5)冷轧过程中,随冷轧压下量增大,中部的第二相尺寸略有减小,冷轧后铸锭组织的不均匀性无法彻底消除;冷轧变形量、冷却速度等因素影响冷轧卷材织构的种类,终轧温度则无明显的影响。(6)冷轧变形量、终轧温度和薄带冷却速度对成品薄带织构含量和制耳率有很大影响,冷轧变形量越大,终轧温度越低,形变织构的α、β取向密度值越大,即形变织构含量越高,制耳率越大;在相同终轧温度条件下,缓冷比快冷的薄带β取向密度更大,制耳率更高;由于带材边部冷却不均匀,带材边部的取向线分布规律性不如中部,带材边部的制耳率高于中部。(7) Fe/Si比低和Fe含量低的3104罐体料具有更高的立方织构含量,制耳率更小,Al(Fe,Mn,Si)相含量更高,化合物颗粒更小,力学性能更合适,应用性能更好。
论文目录
摘要ABSTRACT第一章 文献综述1.1 铝易拉罐罐体用铝合金的应用及发展1.2 3104合金物相调控技术研究1.2.1 化学成分对化合物相的影响1.2.2 铸造工艺控制初生相和溶质分布1.2.3 均匀化热处理1.2.4 塑性变形改变化合物形态1.3 3104合金织构和制耳的控制1.3.1 织构的定义1.3.2 制耳的形成1.3.3 再结晶织构形成机理1.3.4 3104罐体料织构和制耳率控制研究1.4 3104合金罐体料熔体净化和铸造工艺1.4.1 熔体处理1.4.2 晶粒细化1.4.3 铸造1.5 铸锭均匀化1.6 热轧1.6.1 热轧过程组织和性能的变化1.6.2 3104合金热轧的流变应力曲线1.7 冷轧1.7.1 冷轧硬化曲线1.7.2 冷轧及回复退火过程中组织与性能变化1.7.3 3104合金冷变形过程组织性能的变化1.8 易拉罐的制造过程1.9 本文的研究目的和主要研究内容第二章 材料与试验方法2.1 实验技术路线2.2 材料制备2.2.1 材料制备方法2.2.2 均匀化退火2.3 试验方法2.3.1 成分分析2.3.2 性能测试2.3.3 微观组织结构观察与分析2.3.4 JMATPRO软件模拟第三章 3104合金大规格铸锭成分和组织的不均匀性3.1 取样和试验方法3.2 铸锭的化学成分偏析3.2.1 铸锭宏观偏析3.2.2 铸锭微观偏析3.3 铸锭横截面上不同部位显微组织分析3.3.1 大规格铸锭横断面的低倍组织3.3.2 大规格铸锭横断面不同部位的晶粒形貌3.3.3 大规格铸锭横断面不同部位高倍组织分析3.4 分析和讨论3.4.1 铸锭凝固温度场对成分和组织分布的影响3.4.2 3104铝合金铸锭中的物相3.4.3 横截面上成分组织不均匀性的原因3.5 本章小结第四章 均匀化对大规格铸锭组织和性能的影响4.1 铸态合金的DSC热分析4.2 不同均匀化处理条件下铸锭组织的变化4.2.1 均匀化处理对铸锭中部组织的影响4.2.2 均匀化处理时铝固溶体中相的析出4.2.3 铸锭均匀化过程中成分偏析和物相变化分析4.3 均匀化处理对铸锭中部硬度的影响4.4 均匀化处理对后续加工材性能和组织的影响4.5 分析与讨论4.5.1 均匀化退火时的组织变化4.5.2 均匀化过程中的枝晶偏析消除4.5.3 均匀化过程中的相转变4.5.4 第二相对再结晶的影响4.5.5 3104合金铸锭最佳均匀化处理工艺的选择4.6 本章小结第五章 大规格铸锭热轧过程中组织性能变化5.1 大规格铸锭热轧过程中的组织变化5.1.1 热粗轧过程中热轧板坯的化合物形态5.1.2 热粗轧板坯不同部位的晶粒5.1.3 热精轧带材的组织5.2 热轧参数对组织的影响5.2.1 不同热轧条件下的织构5.2.2 热精轧过程的织构变化5.2.3 热精轧终轧温度对组织的影响5.2.4 热精轧卷冷却方式对组织的影响5.2.5 化学成分对热轧带材织构的影响5.3 分析与讨论5.4 本章小结第六章 冷轧对合金带材组织结构和性能的影响6.1 实验方案6.2 冷轧过程中组织变化6.2.1 晶粒形貌变化6.2.2 冷轧过程中第二相的变化6.2.3 不同冷轧厚度的微观组织6.3 冷轧过程中力学性能的变化6.3.1 硬化曲线及不同厚度的制耳率6.3.2 不同冷轧厚度、不同取向的力学性能6.3.3 终轧温度和冷却速度对力学性能和制耳率的影响6.4 终轧温度和冷却方式对织构的影响6.4.1 终轧温度和冷却方式对织构影响的实验结果6.4.2 分析与讨论6.4.3 不同终轧温度和冷却方式下的微观组织6.5 冷轧变形量对织构的影响6.5.1 冷轧变形量对织构和制耳率的影响6.5.2 分析与讨论6.6 本章小结第七章 合金成分、组织和性能对罐体应用性能的影响7.1 3104罐体料的性能指标与制罐应用性能7.1.1 3104罐体料的性能指标7.1.2 制罐厂的性能评价指标7.1.3 罐体料的技术指标和成品罐的技术指标7.2 成分、组织结构与性能对应用性能的影响7.2.1 产品的力学性能及制耳率7.2.2 产品的显微组织7.2.3 产品中化合物的XRD分析结果7.2.4 产品的织构分析7.2.5 两种产品的实际生产线冲制结果7.3 分析与讨论7.3.1 织构与制耳率的关系7.3.2 物相的尺寸、分布、种类与使用效果的关系7.4 本章小结结论参考文献致谢附录1 攻读学位期间主要的研究成果附录2 论文研究生产现场
相关论文文献
标签:合金论文; 大规格铸锭论文; 铸锭均匀化论文;
罐体用大规格3104铝合金材料制备、组织与性能研究
下载Doc文档